Common Applications of Borescopes
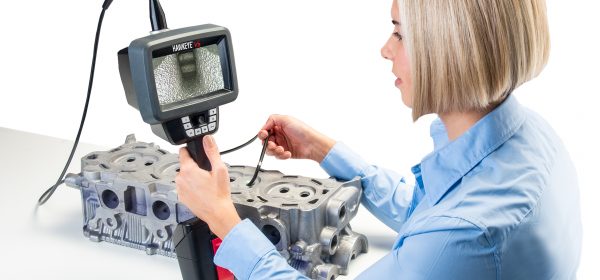
February 15, 2021
One of the most exciting developments in camera history is the borescope. These fantastic devices combine so many ideas that were once science fiction into a present-day wonder. A borescope is essentially a tiny, live camera mounted on either a flexible length of fiber optics or at the end of a rigid tube, much like a focal lens on photography or video cameras.
With these devices, industries and businesses around the world can investigate hidden spaces within the elements of their field. Many common applications of borescopes keep workers and general consumers safe, often in subtle and unappreciated ways that are nonetheless essential.
Borescopes in History
The borescope first came to the market in the 1960s to assist in inspection work. Narinder Kapany and Brian O’Brien, two American scientists, are credited with creating the first model. It had a rigid tube design and could only fit into specific tunnels due to the singular shape and size. Since then, many advancements have come about to tweak and polish the original design.
Nowadays, we can enjoy a wide range of useful borescopes. Each has a specific diameter and specifications to make it ideal in inspecting different components and elements of machines and environments across several industries. Many high-quality professional borescopes and tools are available on the market, such as our line of Hawkeye borescopes.
In 1930, a German medical student named Heinrich Lamm took the first fiber-optic image. Fiber optics are thin strands of clear material that transmit light through their entire length. This characteristic makes something like a borescope LED light source an excellent option for many functions. With this fiber-optic technology, an image can project through a bundle of these fibers to a larger display that is more convenient and practical. The applications are instantly apparent, and work has continued nearly nonstop on the technology ever since.
Scientists and engineers continued to explore fiber optics for a few more decades. Then, in 1964, not long after the first borescope’s invention, the marriage of fiberoptics and the borescope concept led to a rapid interest in and application of flexible borescopes and endoscopes.
Cast Component Inspection
One of the earliest uses of borescopes was to inspect the interior of rigid components. The most common applications of borescopes still accomplish these tasks today. One of the most prevalent and widespread applications of borescopes was to inspect the quality of cast elements such as pipes. Interior portions of machinery have to be as precise as the exterior.
A borescope inserted into a tunnel can identify burs and other metal flaws that require immediate maintenance and correction. They can also travel down the length of a pipe and help specialists search for signs of stress, cracking, or other manufacturing errors. The use of borescopes in manufacturing provides quality control for finished products and can help identify possible improvements in the manufacturing process. Evidence of frequent flaws points to an error in metal composition, material heating and cooling, or even a handling issue that might result in different types of defects in the final product.
People used rigid borescopes used as early as World War II to inspect the bores of firearms. While most people wouldn’t think of munitions as delicate, they are another very precise invention. Slight shifts in angles, as well as ridges and burs, can create dangerous jams and blockages. Bores with flaws and fractures are also very dangerous and can result in misfiring and other serious problems. As such, to this day, companies rely heavily on borescopes in the manufacturing of firearms—whether they are for military use, hobbyist target shooting, or hunting arms.
Heavy Equipment Maintenance
One of the most popular uses for borescopes is in industries that utilize heavy equipment. Some of the most common businesses include automotive mechanics, construction, aviation, and, as mentioned, the crafting of firearms. When it comes to fields like automotive and airplane manufacturing and maintenance, nothing can be too precise. During the creation process, every inch of every tube, wire, piston, and valve requires careful and methodical impaction for flaws and issues, typically with a variety of borescopes.
While not yet assembled, one can use a rigid borescope of one or many camera diameters to explore these components visually. Once assembled into a complete automobile, public transit system, turbine engine, plane, or jet, things get more complicated. While mechanics and motor enthusiasts may occasionally deconstruct engines entirely to clean and optimize them, this is typically an all-day or multi-day project, which, of course, makes it thoroughly impractical.
Imagine taking your car to a mechanic to check out a strange noise, only to discover that they took it down to nuts and bolts, costing you significantly more money in unnecessary labor and putting your car out of commission for days or possibly weeks! That is a world without borescopes, as these handy devices are crucial for saving time and money when it comes to diagnosing engine trouble of any sort.
Rather than pulling an engine apart any time there might be a problem, a type of borescope—rigid or flexible, depending on the type of engine and the location one needs to probe—can move around the gaps and spaces to look for any problems. This live view lets a mechanic probe every inch inside and out of an engine to ensure that there are no stress points as components wear through continuous use. The ability to remotely explore finite spaces has made the borescope a must-have tool in almost any industry where precision is a critical component.
At Gradient Lens Corporation, we know borescopes. With experience manufacturing, designing, and selling over eighty models of borescopes for use across many industries, we are more than able to get the necessary product into the right hands. We have been specializing in these amazing pieces of technology for over twenty years and are at the cutting edge of fiberoptics and camera technology evolution. All this boils down to top-notch, professional-quality borescopes that you can rely on every time for efficient imaging and inspecting.
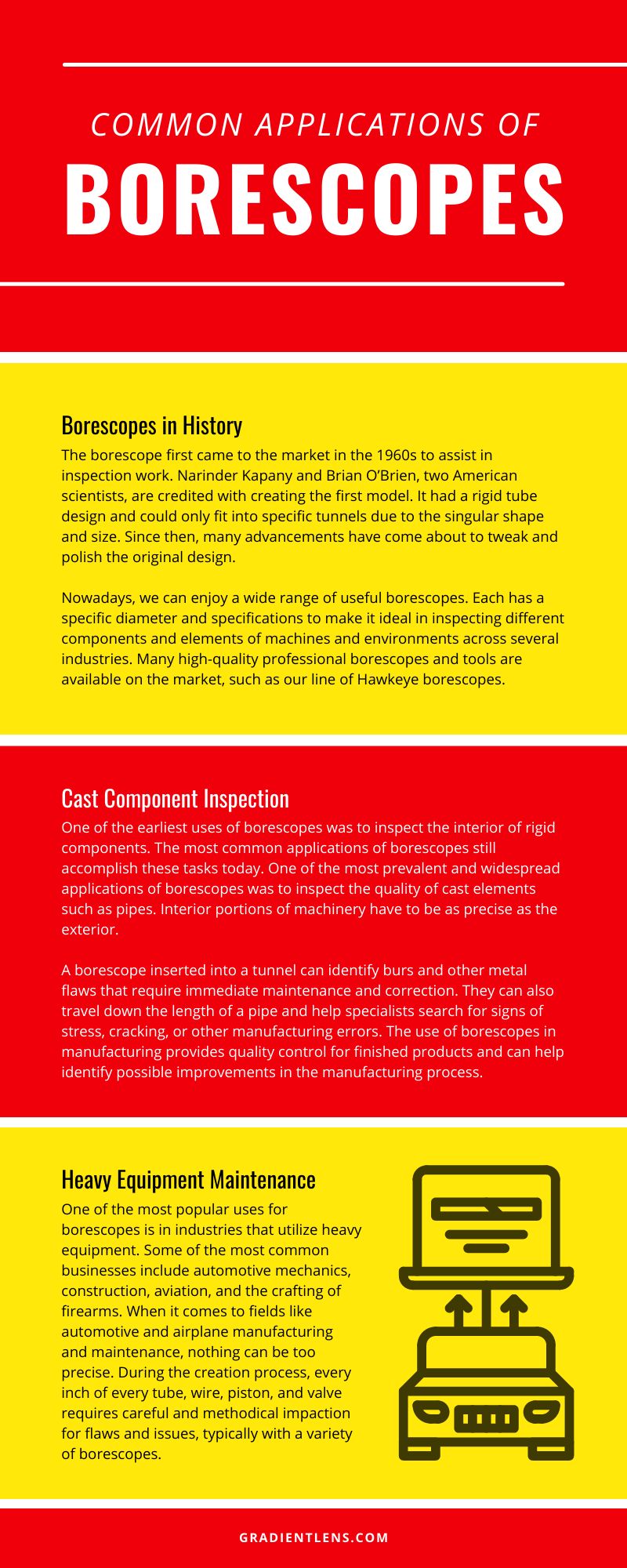