How a Borescope Inspection of Aircraft Turbines Works
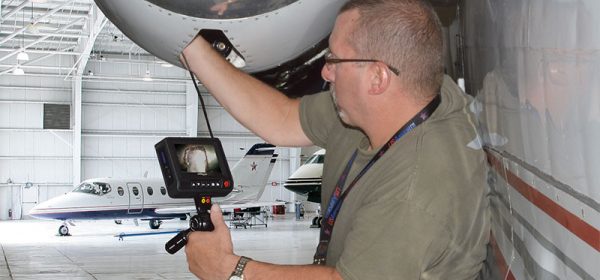
March 25, 2021
Modern-day flight is a wonder of engineering. However, even with current advances in technology, the science behind flight isn’t perfect. As a result, it takes dedicated professionals to take care of the crafts that are essential to moving people and goods across vast distances. Though a mystery to most of us, mechanics have no trouble explaining how a borescope inspection of aircraft turbines works. As an integral part of many aircraft, it takes serious knowledge and equipment to properly search for flaws in turbines.
What Is an Aircraft Turbine?
A turbine is a machine that generates power through a continuous spinning motion. Typically, motion is driven by a current of air, steam, or water. Turbines feature many small vanes that tightly overlap. When the driving elements collide with these vanes and the air attempts to rapidly move through the vanes, a turning motion is created.
In aircraft, the turbine is typically located behind the combustion chamber. First, the prop rotates, forcing air into the compressor where it is pressurized. Once compressed, the air moves into the fuel chamber, which causes the essential chemical reaction. Gases are created by this combustion which again expands the molecules of air and fuel. The expanding mixture is then forced through the turbine, creating the necessary revolving movement. In turn, the generator creates power through a motion that keeps the compressor running.
Problems With Turbine Engines
The science behind the almost entirely self-propelled power of an aircraft engine is amazing. However, it’s not without flaws. Foreign objects can get dragged in along with air, causing damage. Besides this, aircraft engines are subject to the same wear and tear as any other machine. Corrosion, faulty parts, general deterioration, and cracks or warping caused by continuous exposure to internal heat from combustion are a few other common issues.
Needless to say that inspecting a machine as compact and intricate as an aircraft engine is no small task. Unlike automobile engines, simply “cracking the hood” will not always reveal every issue, let alone the entire spectrum of components. Disassembling an entire plane is hardly practical, either. Instead, engineers traverse the interior depth of internal working via remote viewing devices.
How Borescopes Help
How a borescope inspection of aircraft turbines works is fairly simple. Most often, a fiber optic borescope is used, as the flexible length of optic cables perfectly bends into tight spaces. Handheld units are ideal for quickly peering into a plane’s turbines. This area of the engine, in particular, must be routinely given a visual check, as it’s one of the hottest running areas in a plane. The vanes of the turbines are exposed to bursts of heat as fuel is injected into the air intake, as well as blasts of fast-moving cool air dragged in by the rotation of the prop.
Transitioning rapidly between extreme heating and cooling puts immense strain on even the most durable of metals. Thus, the vanes of turbines can develop dangerous fractures that, if left untended, can result in major damage, if not a total failure. Using a borescope, the mechanic can look closely at every inch of each vane to ensure breaks never occur.