Kreisler Industries
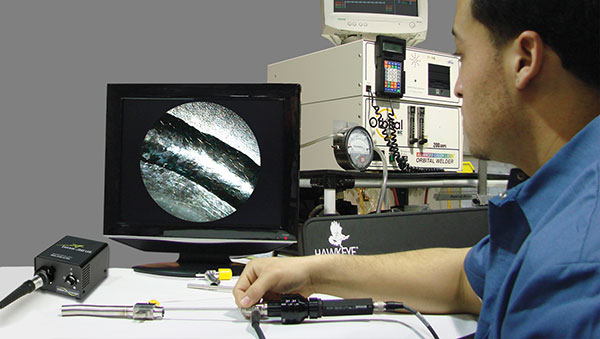
When you’re building components for commercial and military jet engines, quality assurance is always on the front burner.
Kreisler Industries, founded in 1914, manufactures tube and manifold assemblies for aircraft engines. Kreisler products show up in aircraft like the Boeing 787 engine and the latest F-35 Joint Strike Fighter. A common characteristic among many of the company’s products is manual and orbital-welded joints.
A build-to-print fabrication company, Kreisler focuses intensely on quality control for the obvious reason of flight safety. Achieving its—and, of course, its customers’—stringent quality requirements is a daunting task in any circumstance. In today’s world of designing for manufacture and implementing lean manufacturing initiatives on the shop floor, Kreisler has found an obvious and practical need to bring technology and increased quality to the operator in the manufacturing cell.
According to Kreisler President Michael Stern, “We call a customer return an ‘escape,’ and no level of escapes is acceptable. The passengers, pilot and crew are all counting on us to perform our inspection correctly in order to eliminate any risk to the safety and well being of the flying public.” For Kreisler, “escapes” are very expensive, both in monetary terms and in customer satisfaction, and the company has set an aggressive goal of zero customer returns in 2008.
Kreisler needs to identify visual defects as early as possible in the manufacturing process. Doing so provides immediate feedback to the welder or welding operator, reduces the cost of rework, and decreases the likelihood of a nonconforming part ever reaching the customer.
To meet its quality requirements, Kreisler has focused on improving its manufacturing process and products with tools like six sigma and lean manufacturing. In addition, to help them better understand customer specifications, all Kreisler’s welders go through a visual training program, with a practical component of visually inspecting actual parts and a technical component of reading specifications and understanding what’s acceptable to their customers. Kreisler even occasionally shuts down its plant for a day just to discuss quality issues. “Kreisler Quality Day” features customer talks and breakout sessions.
Finally, Kreisler employs what Stern terms “very aggressive borescope inspection” in order to detect defects earlier in the manufacturing process. Kreisler uses Gradient Lens Corporation’s Hawkeye Precision Borescopes to inspect weld joints to ensure the quality of the weld is acceptable and that the part is flight worthy. All of Kreisler’s welders and weld operators have been trained in visual inspection requirements and perform borescopic inspections.
In most cases, operators employ orbital welding with an integral filler metal, machined directly into a fitting. They examine each weld to ensure there’s no lack of penetration of the weld bead through the parent metal, which typically is titanium, nickel or stainless steel. For instance, the key factor in making high-quality welds in titanium is cleanliness. Thus, inspectors look for weld porosity or contamination.
Performing a borescopic inspection on the first work piece gives the welder or weld operator immediate feedback on whether the penetration is acceptable without waiting for x-ray results. This allows the operator to change welding parameters as necessary to ensure a conforming part.
Kreisler used to have just one borescope, but the increased complexity of its assurance program demanded additional instruments. As well, Stern says, “With its low-cost lens technology, Gradient has driven down the cost so we can afford to bring borescopes to the cell level and the welder.” Ultimately, according to Stern, Gradient has in many ways helped Kreisler bring final inspection into the manufacturing cell.
Kreisler is putting another wrinkle in the inspection process with its addition of video systems attached to borescopes. Explains Stern, “The video systems provide blown-up views, so they give inspectors an enhanced picture of welded joints. Welders can just lay down a tube and twirl the scope around to easily and quickly inspect their work. Also, the video system has become a great tool for welder training on visual requirements.”
Kreisler also inspects all welds with x-ray equipment, and an x-ray Level III inspector may use a borescope to confirm something s/he notices on the x-ray image. Kreisler then sends each part for a final inspection, where the inspector may use the borescope to verify the weld meets specification. The company tracks quality metrics like customer returns and defect trends. For instance, a nonconforming part is evaluated by Kreisler’s Quality Clinic, which documents a rework procedure signed by quality and manufacturing personnel.
Before borescope inspection, Kreisler’s alternatives to visually inspect parts were a magnifier with a light source or x-ray, which, says Stern, “gets a lot more expensive if we wait to inspect and correct a part at x-ray stage.”
Ultimately, adds Stern, “Achieving the highest level of quality is a continuous effort, and whatever we can do to increase efficiency to the manufacturing cell we will do.”
To find out more, visit www.kreisler-ind.com and www.gradientlens.com.